
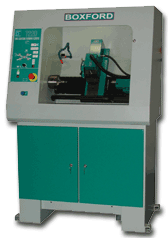
Move it to you location, and get it close to the area you would like it to set. Once you have it on the shop floor, you are well on the way. If you have the light end of the machine, then maybe two people can let it down slowly to keep from having an abrupt drop. Stop the unit when the back side reaches the drop off. Let the lathe roll out over the drop off as far as you can to reach the balance point, and then gently let it rock down to a waiting pipe and continue forward. The 2" drop shouldn't be a huge deal, but be cautions as this is where it can run away from you. Again, have the heavy end in the direction of travel. Once you have the machine turned the direction you need, then move it across the kitchen floor until you reach you next step. Be mindful that you don't want to tip the unit, and this will be the most likely place it will happen. The turn will be some careful persuasion to the unit to get it to slide on the pipes. I think I would have the heavy end go in first. Place your rollers under it and move it into the kitchen and prepare for the turn. Also know that there will not be enough strength in the plywood to hold the weight of the machine, but this will give you a safety margin in case things go awry.īring your lathe to your first doorway, and then pick it up with a hoist (assuming one can fit there if not, then you might look at breaking the cabinet and lathe apart for the move) and set it up on some blocks that are of the same height as you kitchen floor. Move one sheet in front of the other until you clear the area needing protection.
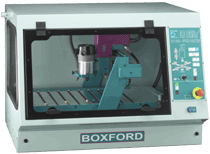
If your floor is fragile, use a couple of sheets of paneling or Masonite to protect the floor. Just place one in front of the machine as you are moving it along. Have enough rollers on hand that the machine will be on three or four at all times. Use some small diameter plastic pipe (PVC here in the states) cut into lengths about 3" wider than the width of the machine as rollers and once the lathe is on the floor you can easily roll it where you need it to go. Once you have it on a flat surface, you will be able to move it around without too much trouble. I think that I would place the whole unit on a sheet of plywood that is not but a slight bid larger than the footprint of the machine, and attach it with some method (screws, bolts, straps,etc).

Two people could do the job, but to play it safe I'd have a third. The only problem this will present is the it will be top heavy! My thoughts on the move are to leave the lathe and stand intact. The roller wasn't in the chuck at the time Me and Ower Gert put this into position one Sunday morning before church using only 4 lengths of 1" angle, a 3 foot pry bar and 17 cups of coffee. Once you have used this method you will never go back to rollers and bits of tube. The point contact will allow it to move as if on rollers and you can go 8 to 10 feet at a time, if you have to go up or down steps use two planks with shorter pieces of bar on them. Get 2 lengths of 1/2 round bar or 3/4" black angle, vee uppermost, drop these down like tram rials and just push the machine along the rails. if you can't get it onto a trolly or such like don't bother with rollers they are a total waste of time, you spend more time poking the band things under then a little. Up a step, thru a door 10 feet to the right etc. If it's anything like Harrison's used it's more like that old Boss White they glued apprentices to steam pipes with.ĭries like concrete and you need a welders chipping hammer or a Kango to get off. does anyone out there actually have experience of taking one of these apart. "1) If the lathe has a gearbox, leave it in place - and try not to remove a lathe from an under-drive stand a compound was used to stop coolant getting into the wrong places and effectively sticks the lathe down once broken the hardened sealer has to be chipped off and the joint remade.Ģ) Apparently the drive belt is continuous and will need to be cut." In principle it seems straightforward, but two points concern me a little. to get it into the workshop it has to go through 2 x single doorways up 2 steps, then down one step, so methinks dismantling it may be the best way forward. Transporting it home should be OK, it can be loaded into my van with a fork lift, at my end we can have the use of an engine lift to get it out. The total weight is over 600lbs so that's the first hurdle. UnderDrive, the motor is in the base / cabinet. There is a wealth of information about these on the web but some of it is a little conflicting, the AUD is the model "A" (Screwcutting Gearbox and Power feeds in both directions) with UD.
